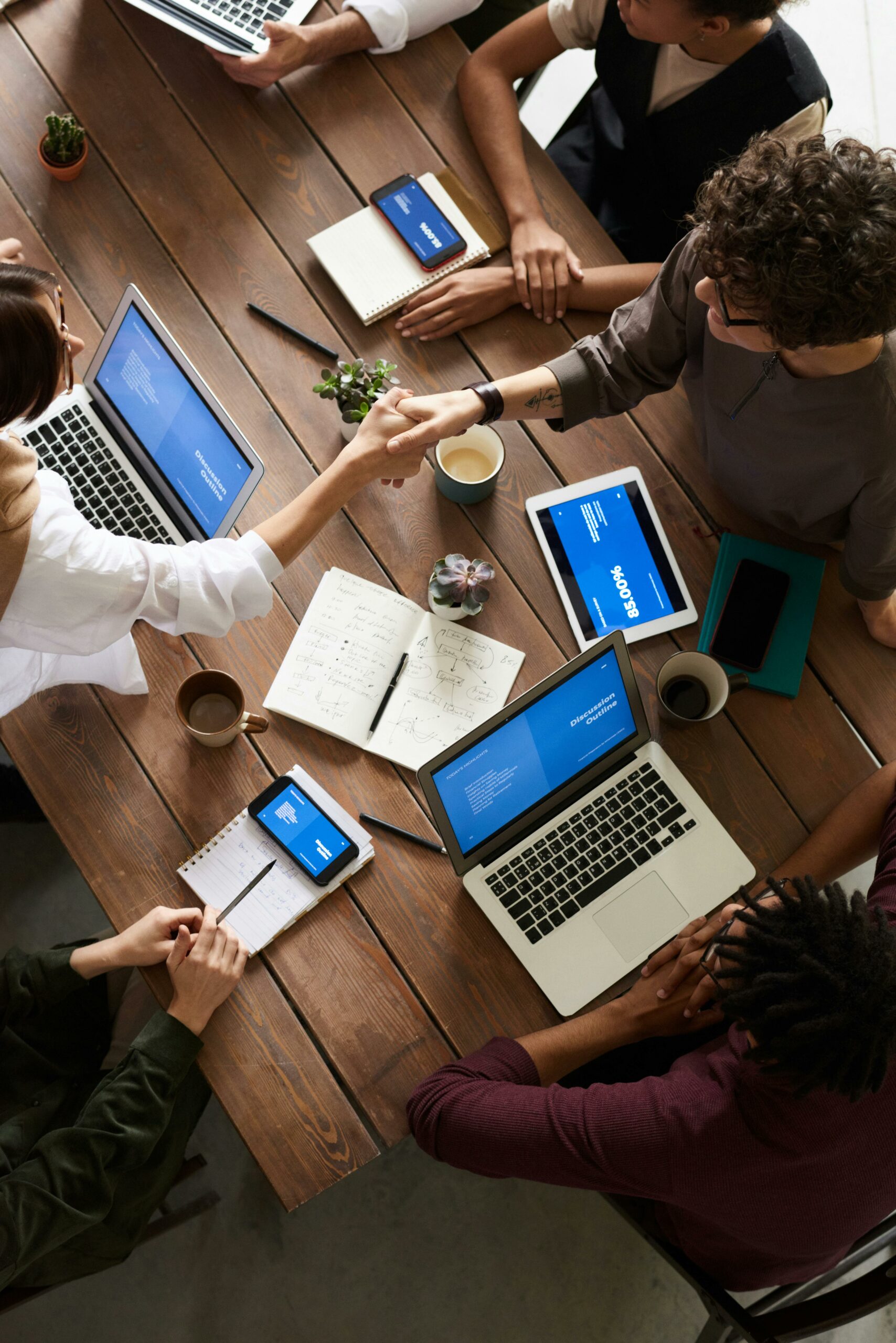
Slim besparen = Slim ondernemen: waarom energiebesparing loont voor het mkb
Energiebesparing
Elke ondernemer weet: controle over je kosten is cruciaal. Zeker in een tijd waarin de...
U hebt het vast in huis: een pak Appelsientje, Taksi, DubbelFrisss of CoolBest. Alle kartonverpakkingen van deze typisch Nederlandse merken komen uit één fabriek: FrieslandCampina Riedel B.V. in Ede. In groten getale: honderdduizenden pakken per dag. Voor de productie ervan is voedselveilige perslucht onontbeerlijk. Met nieuwe compressoren en een ‘Inteligent Flow Control’ van Klimaatplein partner Geveke is er ruim 15% minder perslucht nodig dan voorheen.
FrieslandCampina behoort tot de vijf grootste zuivelconcerns in de wereld. Bijna alle 100 fabrieken maken producten van melk, zo niet de fabriek in Ede. Die maakt vruchtensappen. De grondstoffen daarvoor komen uit alle delen van de wereld. Die grondstoffen worden volgens receptuur in enorme tanks gemengd en daarna in kartonnen verpakkingen gepompt, daarbij wordt perslucht gebruikt.
Vorig jaar waren de compressoren toe aan vervanging. Een gespecialiseerde projectgroep ging met diverse persluchtleveranciers om tafel om de beste oplossing te bespreken voor het verbruiksbeeld dat al jaren wordt bijgehouden. Theo van Helden, manager Onderhoud: “We hebben voor Geveke gekozen omdat het een professioneel bedrijf is en we goede ervaringen hebben met eerdere projecten. Geveke was een bestaande leverancier en deed ook het onderhoud van andere merken compressoren. We waren gecharmeerd van de oplossing om naast twee vaste toerental compressoren een toerengeregelde compressor te plaatsen. We hebben er vervolgens zelf voor gekozen extra te investeren in een vierde compressor om het energieverbruik nog lager te krijgen. Alle compressoren draaien daardoor bij elke persluchtvraag in hun efficiënte gebied. We gebruiken nu zo min mogelijk perslucht voor de productie van een pak sap. Duurzaamheid is voor FrieslandCampina een belangrijk issue en dit project maakte onderdeel uit van ons energiereductieprogramma.”
De compressoren zorgen er samen met de nieuwe IFC (Intelligent Flow Control) voor dat er ruim 15% minder energie wordt verbruikt. Met de IFC kon de druk in het net bijna een bar omlaag. De IFC houdt de druk altijd constant door een regelende klep die het buffervat actief een rol laat spelen als het verbruik fluctueert. “Bijkomend voordeel is dat we door de stabiele druk ook de ventielen en cilinders van machines nauwkeuriger kunnen afstellen. De schakelbetrouwbaarheid is daardoor groter geworden en dat betekent minder uitval van productie,” aldus Van Helden.
Bij het productieproces gebruikt de sapfabriek water als asafdichting. Na gebruik is dat water nog van drinkwaterkwaliteit en wordt het gebruikt om mee schoon te maken. Het water wordt eerst opgevangen en tegenwoordig via een warmtewisselaar voorverwarmd met koelwater uit de compressor. Van Helden: “Daarmee winnen we de helft van de energie terug die we anders in het opwarmen van water zouden stoppen, zo’n 80 kW. De investering in het complete warmteterugwinsysteem verdienen we binnen vijf jaar terug.”
Als ondernemer zelf aan de slag met energiebesparing? Hier vindt u enkele praktische tips voor besparen in een productieomgeving.